- Home
- Knowledge library
- The benefits of using air scrubbers in pig buildings
The benefits of using air scrubbers in pig buildings
Air scrubbers are recognised as a Best Available Technique (BAT) for the reduction of ammonia from pig buildings. They can also reduce the carbon footprint of pig production with heat recovery.
How do air scrubbers work?
Air scrubbers use fans to draw air from the buildings air space into the air scrubber. Inside the scrubber is a series of screens and water curtains that remove dust, ammonia and other gases before the clean air exits through an exhaust.
Two different technologies are available:
- Chemical scrubbers: These use an acidic solution to bind the ammonia as ammonium sulphate. This requires the handling, usage and storage of sulphuric acid, therefore the Control of Substances Hazardous to Health (COSHH) guidance and procedures must be followed.
- Biological scrubbers: In this system, the vertical screens are populated by bacteria that bind the ammonia and utilise it for their own growth and reproduction. Rather than chemicals, it is the bacteria that remove the ammonia. Be aware bacteria can be highly sensitive to changes in environmental conditions.
The differences between chemical and biological air scrubbers
Each system has its pros and cons and should be assessed together with an experienced installer as each installation is unique.
In either case, the primary role of an air scrubber is to reduce ammonia. However, most systems utilise some form of heat recovery, which can be used to offset heat requirements in the farrowing and weaning accommodation. This recovered energy lowers the carbon footprint of the farm and offers a return on investment through lower energy costs.
Air scrubbers are recognised as Best Available Technique (BAT) in the BREF documentation, offering a 70–90% reduction in emissions. The use of air scrubbers to limit ammonia emissions could be seen as a useful mitigation solution for permitted sites, those looking to meet local planning conditions or anyone simply wanting to reduce their environmental footprint.
Video provided with permission from Inno+ and Big Dutchman as an example of air scrubber technology.
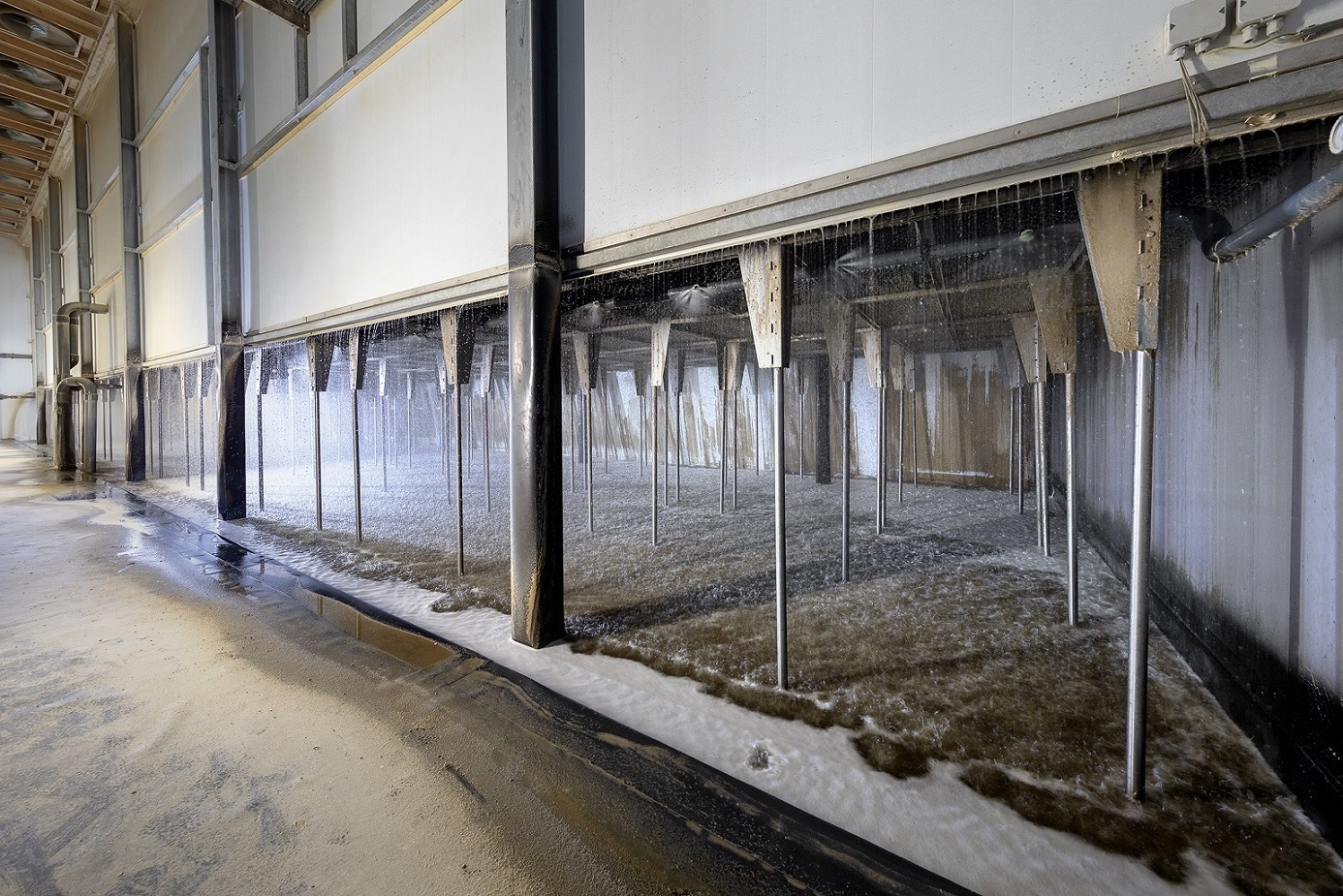
© Inno+
Heat recovery
Heat recovery makes use of a heat exchange system. Warm water from the air scrubber is compressed in a pump to raise its temperature and then passed over pipes containing cool water from the building's heat system. The heat passes from the air scrubber to the building's heat system, which can then be used to heat farrowing pads, buildings and weaner accommodation.
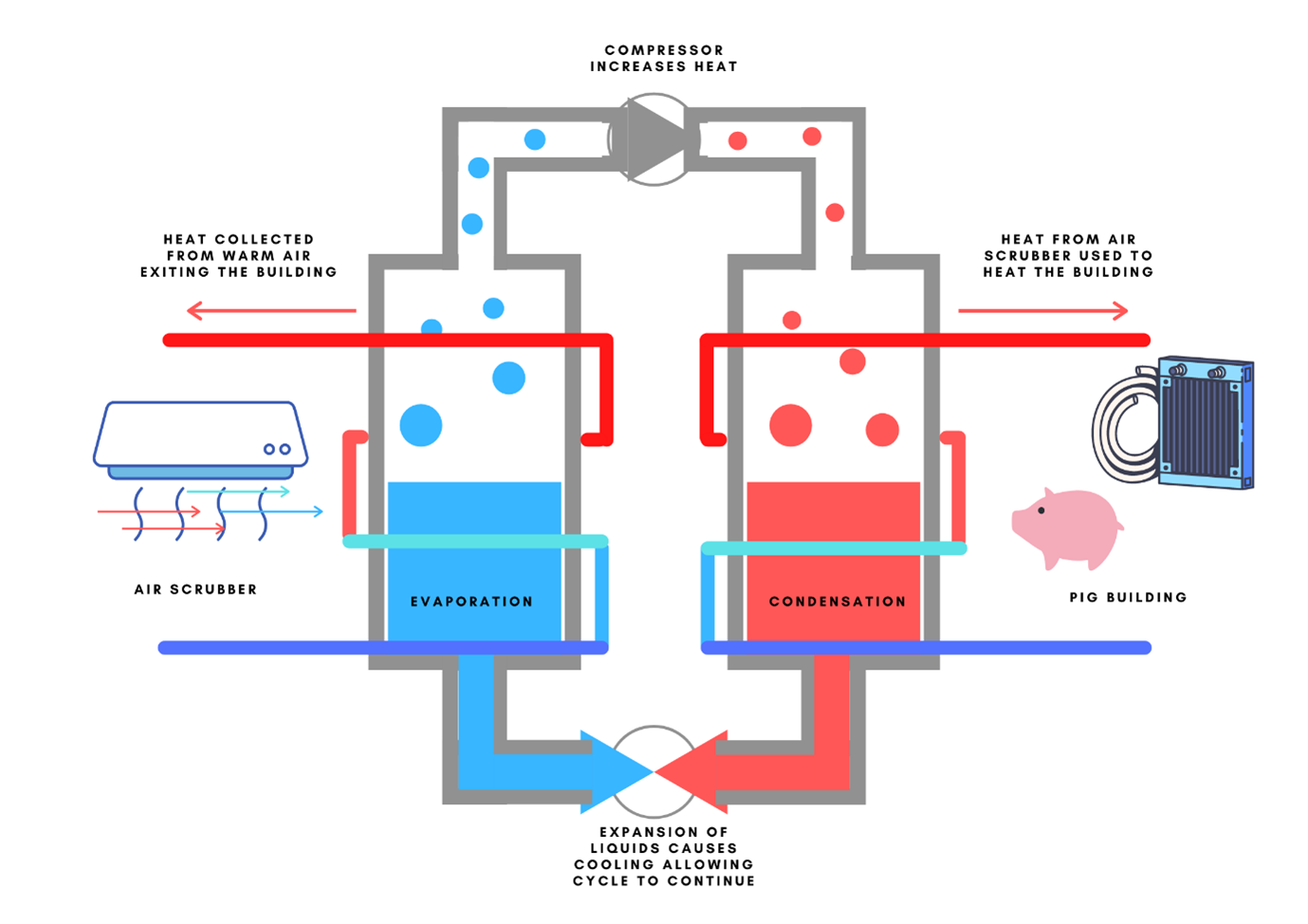
The main reason for installing an air scrubber may be to reduce ammonia, but they also offer benefits such as:
- Saving energy
- Reducing your carbon footprint
- Offsetting your energy costs and offering a return on investment (ROI)
- Opportunities in providing public goods
GrowSave: a knowledge exchange programme helping farmers save energy
Installing an air scrubber
It is recommended that you install air scrubbers as part of a new building. Retrofitting involves substantial compromise and additions to an existing building. This could result in recuded effectiveness and other unforeseen complications.
Air scrubber technology tends to be modular, with each module clearing a specific volume of air per unit of time, e.g. litres/hour. With modules shipped in 20ft or 40ft containers, multiple modules can be installed in single containers providing increased capacity within the same size container.
Most scrubber systems will also include a 'plug and play' control room as part of the package so that the system is ready to operate once connected to power and water.
As each site and system varies, additional buildings or storage spaces are provided separately by the farm. This includes chemical storage and handling facilities so that the farm can follow local chemical storage and handling legislation such as COSHH.
When installing an air scrubber with heat recovery technology, plans must be made for the heat that is recovered. This may require further investment in water heating pads for farrowing accommodation or changes to heaters in weaner and other housed accommodation. It is common for systems to preheat the oncoming air through a heat exchanger to maintain a constant temperature for the pigs.
Standards governing equipment and installation
Not all systems conform to clearly defined standards on flow rates and ammonia removal. As the installation of this technology is often associated with permitted sites, it is advisable to ensure that your installer produces equipment and installations that meet a recognised quality standard. An example would be:
- BWL 2008.01.V6 – While the standard is in Dutch, it describes the flow rates and ammonia removal required to support a 70% reduction in ammonia emissions
Case study: what’s my return on investment?
A finisher farm in the Netherlands installed a biological air scrubber to their 3,000-place finisher unit. Find out about the benefits and return on investment in this case study.
Useful links
Find out more with our range of resources relating to both ammonia reduction and energy efficiency in the pork sector:
Slurry management: Our slurry hub is home to all of our resources on slurry management
Slurry cooling: For a guide on slurry cooling, installation options and supplier directory
Covering slurry stores: Solutions for compliance
Topics:
Sectors:
Tags: