- Home
- Knowledge library
- Youngstock housing case study – Cobblers Farm
Youngstock housing case study – Cobblers Farm
Cobblers Farm is managed by Rob Collins. He rears dairy beef calves using an all-in, all-out (AIAO) system. Rob and his wife, Hanna Moule, purchased a 43-acre block of land with a single farm building on it in 2013. Hanna has expertise in planning, and between them they secured permission for a small livestock unit with an adjacent dwelling.
Rob and Hanna spent two years looking into the various options for calf supply and physical systems to house them. They considered five systems but came back repeatedly to Simon Fryer at Meadow Quality and Joff and Emma Roberts, who import igloo systems. Rob gives them most of the credit for what has emerged on-site.
Rob said that although his father had been rearing calves 30 years previously, he realised that the modern requirements were completely different. The current approach had to be completely professional. The first building went up and was ready for the first intake of calves in March 2018, just as the Beast from the East arrived.
The aim was to run several crops of calves through before increasing the scale of the project on the basis that a single 60-calf set-up was not the best option. The first house takes 60 calves, with a target of five crops per year. After eight crops Rob, has decided to put up a second unit on the other side of the rearing shed.
The building in detail
Building specifications
The system design for each shed is based on four igloos under a permanent mineral fibre roof. A concrete floor with three-way slopes was put in to ensure good drainage, with a centre drain channel leading to a settling tank.
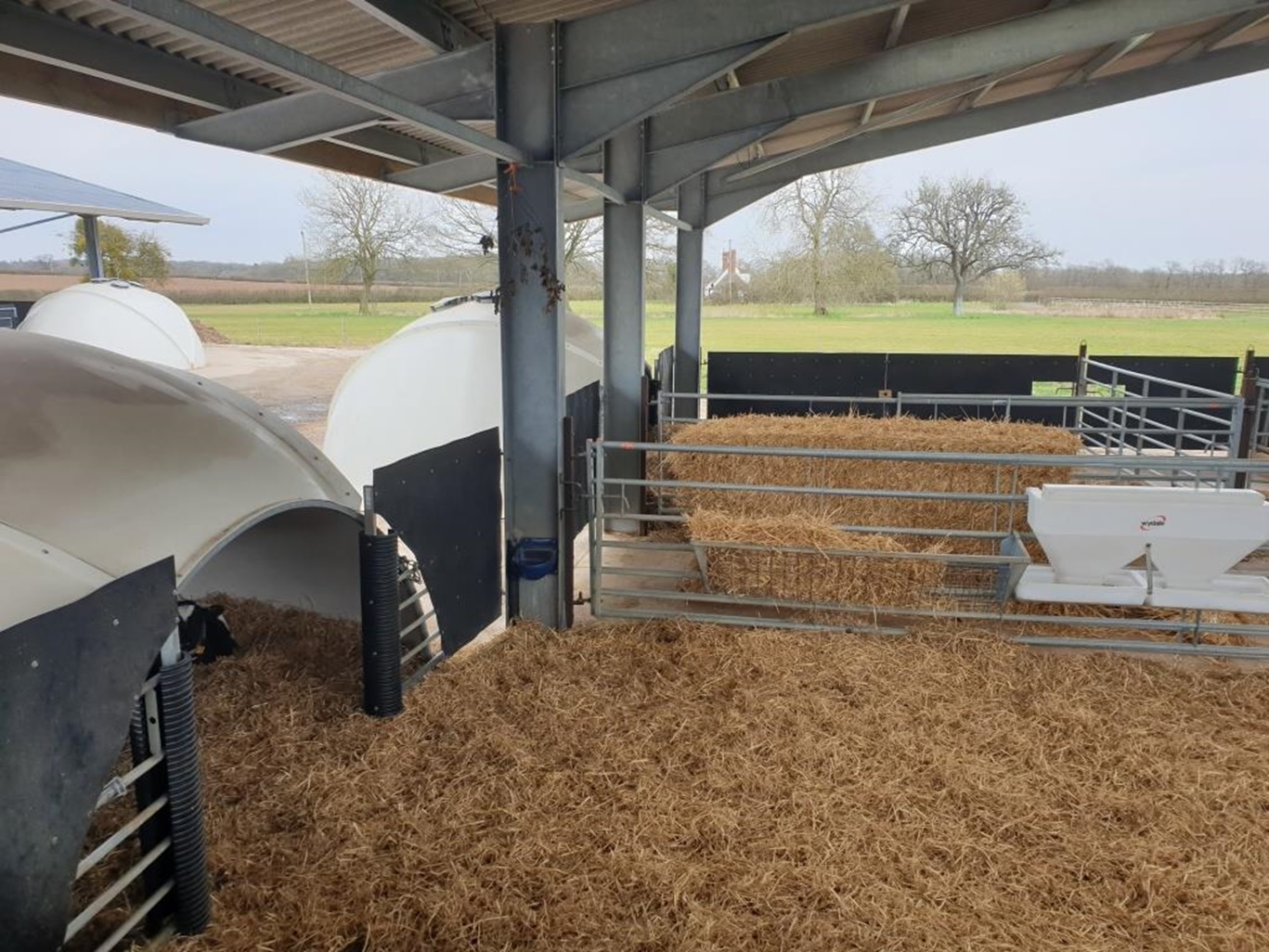
The building is mostly open with no cladding below eaves height. Stockboard sheeting is on all pen gates on the perimeter to prevent draughts at calf level. There are no flaps below the gates on the calf unit. However, flaps are fitted on the adjacent rearing unit. All part-gates on either side of the igloos are also covered with stockboard.
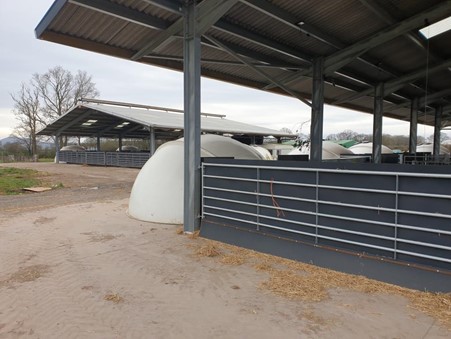
The building has four bays with a large 2 m overhang, providing protection from the elements. The first 5 m bay is for storage and cleaning. The second 5 m bay is for calves, then a 3 m aisle for separation and a final 5 m bay for calves.
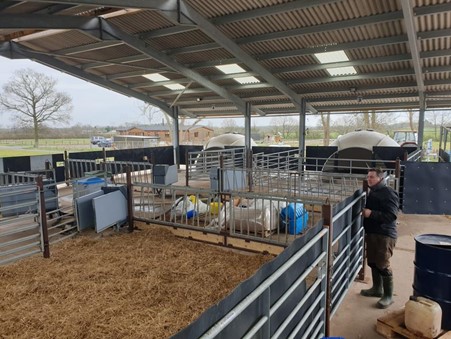
The roof has a covered open ridge but no upstands.
Additional protection from the wind is provided by big bales, when required, arranged to the east or west of the four pens. These can be put up or taken down in a matter of hours and provide a level of flexibility on the exposed site.
Internal layout
The core of each pen is an igloo facing into the centre of the building. There are gates on four sides. Each igloo has a triple vent (as supplied), which gives a useful stack effect inside the igloo when there is no wind-driven ventilation.
Two pens are arranged on one side of the central passage and two on the other side of the passage. Both sets of pens are separated by a 3 m gap, so there is excellent visual contact between calves but no close contact between pens. This space is used for access to each pen and placement of big-bale straw for immediate use.
Feeding is with automatic milk feeders, and water bowls are supplied by filtered, pumped water collected through rainwater harvesting. Solid feed is provided in Wydale feeders.
Building blueprints
The blueprints of Cobblers Farm have been drawn up (see below). These have not been produced by architects and have been created by AHDB to reflect the design on the ground. They should not be used as complete plans, and you should always seek the advice of a qualified architect before designing and constructing buildings.
Cobblers Farm floor plan – Milk shed
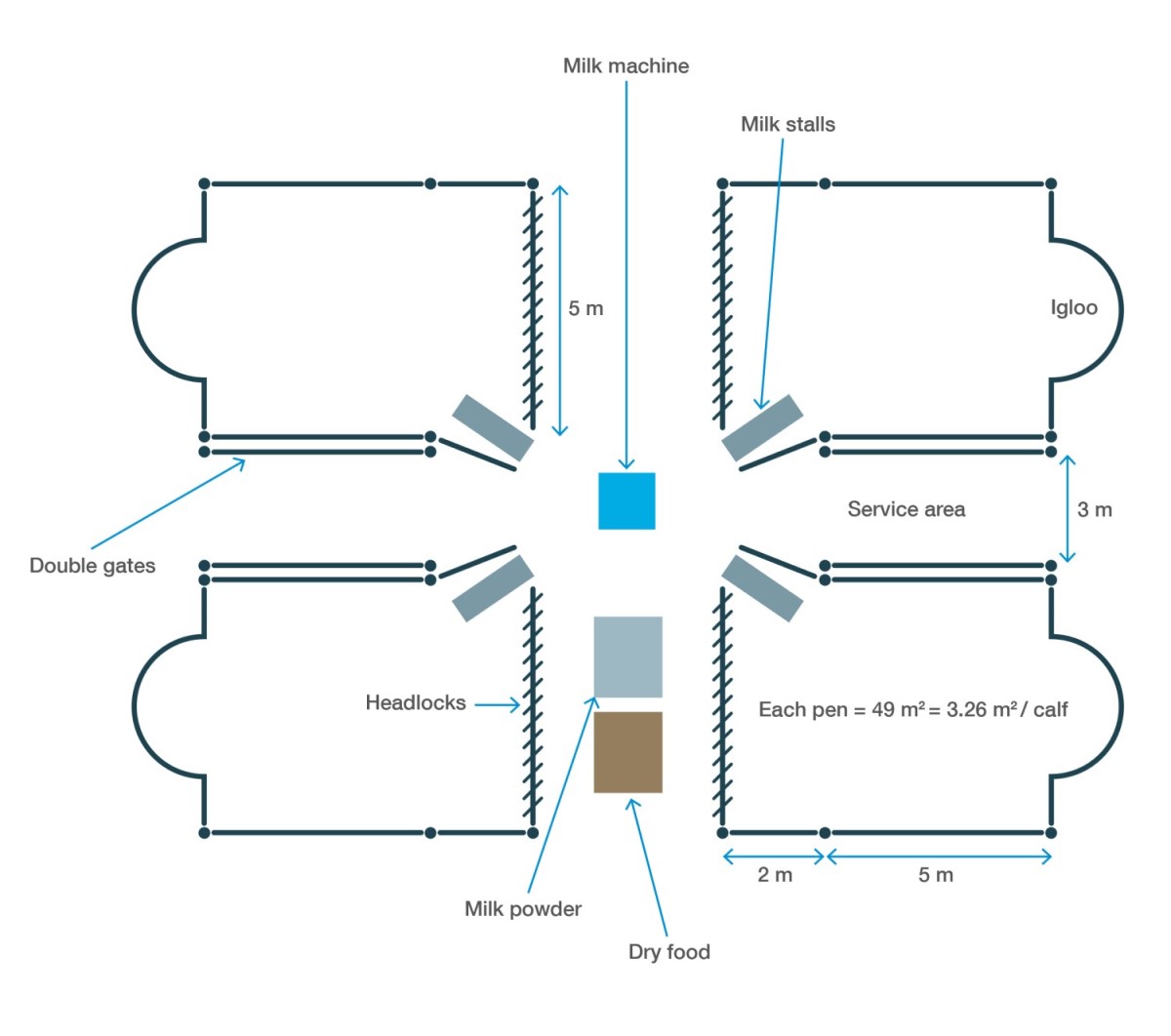
Cobblers Farm floor plan – Weaned shed
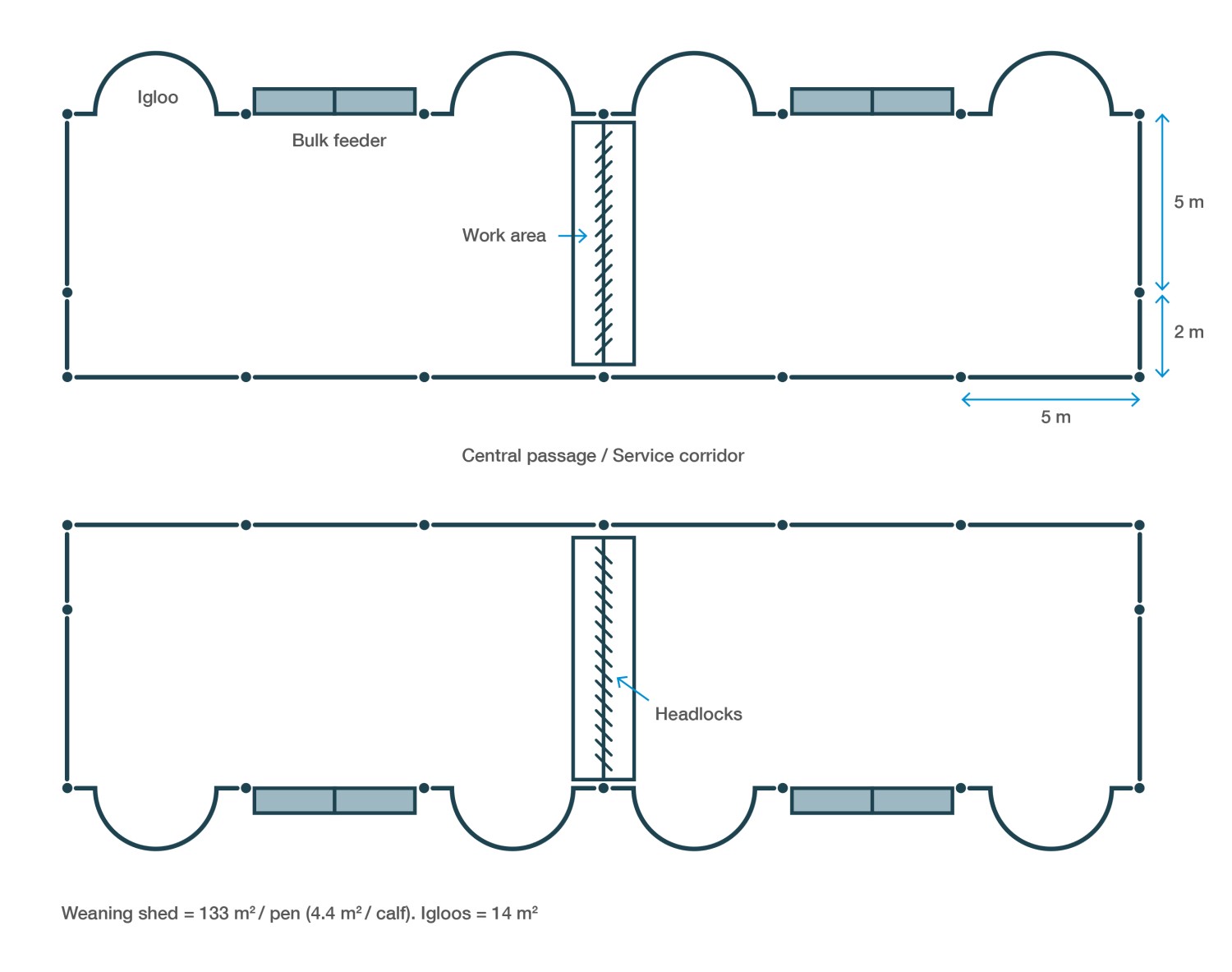
Calf management
Calves are brought to the building at 30−35 days old, mostly from known producers. Calf flow is managed by Meadow Quality. Calves are kept in groups of 13−15, depending on the supply. The pen will have been cleaned, disinfected and left to dry since housing the previous crop of calves.
When the calves arrive, they weigh around 65 kg, and the aim is for them to leave the second stage building at 135 kg.
Calves are weaned off milk and then moved, in their groups, less than 20 m to a similar space for the grower stage, post-weaning. The space has a larger area than the calf unit but overall uses the same design, with a bespoke concrete floor and one igloo for each pen.
The rearing shed was put up and completed in April 2020. Rob has high praise for the team who completed the concrete floor just as the quarantine for COVID-19 was kicking in. Attention was specifically paid to the floor slopes, making sure that drainage was good. Calves still have free access to an igloo in the rearing stage. The rearing shed has a very similar pen and feeding layout to the milk-fed calves’ shed, with a roof cover on a steel frame and no cladding below eaves height.
Calf health
There are no isolation pens. The policy is to get in quickly, and both Rob and Nicky are extremely keen to spot a calf that shows any sign of going off colour. They aim to identify a sick calf before there is a drop in intake at the automatic milk feeder (AMF).
The sick calf protocol at the farm is:
- If off-colour/slow or poor feeding, and temperature is below 38.7°C, give non-steroidal anti-inflammatory
- If showing symptoms and temperature is above 38.8°C, a non-steroidal anti-inflammatory and an antibiotic
With calves being reared in larger groups, the opportunity for disease to spread is significant, so action must be quickly taken.
Calf feeding
Upon arrival, calves are given milk through a Wydale feeder with teats. They receive 6 litres per day (L/d) at 190 g per litre (g/L) milk replacer to a concentration of 819cc.
At 47−53 days old, when the calf will have spent 12−15 days on the farm, this volume drops to 4 L/d. Over days 20−30 on the farm, this is slowly reduced daily to 0 L/d, with the concentration also being lowered over this time from 190 g/L to 150 g/L milk replacer.
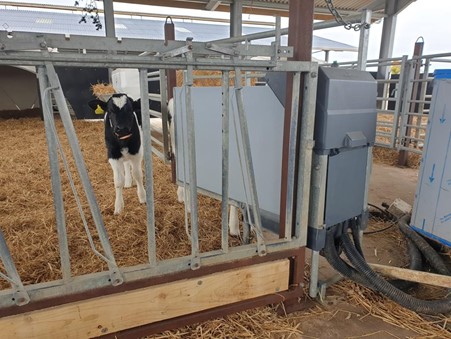
The frequency that the calves can access milk through the feeder is limited, with 3 L fed every 12 hours. However, each occasion is limited to a maximum of 1 L per hour.
Teats on the AMF are given an automatic external rinse after each calf and each feed, with teats being replaced between every batch of calves.
Straw is fed as roughage from day 35 when calves enter the unit.
Water for the calves is harvested as rainwater, which is pumped through an organic filter and, on the output side, through a UV filter. Initial advice on how to set up the system was poor, and the original filter and pump system was suitable for a dwelling instead of a livestock premises. However, this has now been resolved. The total cost, including gutters, tank, pump and filters was £9K.
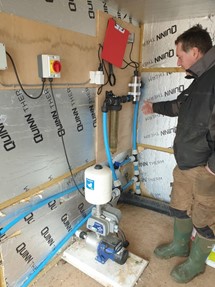
Biosecurity
With calves being reared in large groups for an AIAO system, specific attention is paid to hygiene. Disease can easily be spread within groups, so good biosecurity is paramount.
Buckets, when used at the point of entry into the unit, are always cleaned after every use. Automatic milk feeders and teats have an automatic external rinse on each AMF teat.
A primary wash-down is done with a steam cleaner, and Rob initially struggled with a biofilm remaining. Now, he also uses a degreaser (detergent) between every other batch of calves that is applied and left in contact for 2 hours. This has improved the removal of the biofilm.
The current procedure between batches is:
- Muck out pens
- Steam pressure wash
- Degrease with detergent
- Second steam pressure wash
- Dry for 24 hours
- Disinfect with a multipurpose disinfectant at an appropriate dilution rate
- Dry for 24 hours
- Disinfect with a coccidia targeting disinfectant at an appropriate dilution rate
- Dry for 24 hours
- Calves in
Labour requirements
The system is run by two members of staff, Rob and Nicky.
Variable tasks are done by Rob, with the daily routine tasks done by Nicky. These include the minimum 1 hour, twice-a-day routine feeding and bedding, rising to 2 hours twice per day at peak times. Nicky does most of the wash down after the farmyard manure has been removed.
Capital cost
The facility cost £1,250 per calf for the total build cost and all penning and feeders.
Thoughts on the facility
Rob adopted the advice of others to keep the size of each individual calf ‘unit’ to 60 calves. It is more expensive to build two units of 60 calves each, rather than one that can take 120 calves, but Rob has no regrets. He feels that there is better a air supply and that it is easier to maintain a true AIAO policy.
There is a 3 m space between the adjacent group pens. This can be considered quite an expensive space, but it guarantees separation and no cross-contamination at floor level. He also added an extra bay to the build for storage.
Rob is very positive about the head yoke system in each pen, which is used for vaccinations and dehorning. This means that Nicky can do routine tasks, including dehorning, in 2.5 minutes per calf. As a rule, they do not have any post-weaning problems.
There is a downside when calves come on-site over a longer time period. If it takes three weeks compared to two weeks to fill the unit, there can be a 30% increase in veterinary costs for the batch. Rob’s current contract also requires calves from specific bulls (as part of a genetics programme), which can extend the time taken to fill the unit beyond the targeted two weeks.
Rob has done the job with sufficient confidence that he is going to expand with another, almost identical, unit on the far side of the grower building. The new unit will have the pipework between the AMF and the feed stations in covered channels in the concrete floors rather than in ducts. The current system has them above ground in part-insulated ducting, but this is extra effort that is not needed. Rob and Hanna are keen not to put the milk delivery pipework in conduits under the floor because the milk pipes do sometimes block.
The AMF will likely be located in the centre of the four-pen layout, compared to the more typical system where the AMF is closer to one pair of pens and then 5 m or so from the other pair of pens because Rob feels that calves in the second pair of pens sometimes do less well.
Any future changes will be adopted to make the daily task of caring for all calves on-site easier for one person in lone working conditions. The focus is on working leanly and giving maximum attention to the calves, instead of wasting time with inefficiencies.
Read more about youngstock housing
Legislation and market requirements
Temperature, humidity and ventilation
Housing layout and construction
Designing housing to feed calves with ease